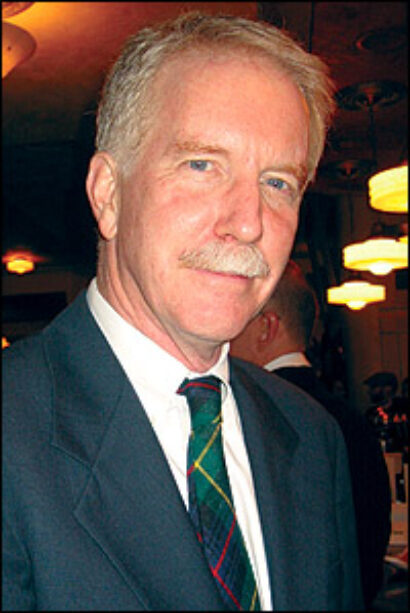
*
One of Kacie Hultgren's duties, as longtime associate of famed theatre set designer John Lee Beatty, is to create the miniature models that illustrate to the director, producer and cast of each production what sort of scenic environment they will be dealing with. Typically, in the past, completing the model took one week, and the work was fairly arduous.
"For the most part, you're using foam core and paper and matte board, and there's a lot of X-Acto blades and putting them together with hot glue," she explained. Beatty insists on a model scale of 1/2 inch to the foot, so the work is meticulous and detailed.
"You're putting together a scale representation of what you're going to see," said Hultgren. "Time schedule is pretty tight. You're trying to get as much detail in the model as you can in the time allotted. That can be tough."
These days, however, the job is considerably less tough, as Hultgren's models take considerably less time, and they are made primarily of one material: Plastic. Making the difference in her work process is the 3D printer, the technology that created three-dimensional objects and has in recent years become available commercially as a professional appliance. Hultgren bought her first pinter in 2011, and the first show she used it on was the Roundabout Theatre Company's 2012 production of the farce Don't Dress for Dinner. She has used the printer on every show she's worked on since, including The Nance, Orphans, The Snow Geese and the current Manhattan Theatre Club production Outside Mullingar.
"It was mostly just timing" she said, explaining the expansion of her set-building toolkit. "The market [for 3D printers] had really changed from DIY projects to machines for professionals."
A 3D printer quickly creates a fully-formed prototype of any object. If a designer wants to make a tiny chair for scenic model, the machine first reads the design and then executes it, extruding layer upon layer of hot plastic until the geometric shape of the chair is complete.
Chairs are a good example of how a 3D printer streamlines a set designer's job. Almost every set of an interior one can think of includes a chair. And usually, it asks for more than one chair of the same sort. (Think of a dining room or kitchen table set.)
"I don't feel guilty asking for 24 lamp posts, and then asking for two more," he added.
A chair takes about 15 minutes to produce. For Outside Mullingar, however, Hultgren didn't limit herself to just individual pieces of furniture, but cranked out large sections of the entire set instead. This was possible because technology has improved in just the two-plus years since Hultgren bought her initial printer. The first printer could produce an object four and one half inches on all all sides. Her new one can create a piece six by five by 11 inches at a much faster rate.
"At first, we only 3D-printed small pieces, like furniture and window frames, incorporated with traditional modeling materials like matte board and bass wood," stated Beatty. "Now, the desktop printers we use are larger, and we can print entire scenic units in scale.
"I printed the complete sets and walls in one chunk," she said of Mullingar. "That took a day."
All these great advancements in set creation are not necessarily noticed by the people set designers need to please, such as directors. "I think for the most part most people look at them and don't really know that they're 3D-printed," observed Hultgren. "They're more interested in the design information in the model. The 3D printing kind of blends into the background."
But director obliviousness won't stop the march of progress. Beatty predicts 3D printers will become more common in the theatre in the years to come.
"We may eventually be building the full scale scenery with a 3D printer," he theorized. "In fact, in a pinch, we've been able to manufacture small pieces of the finished scenery with a 3D printer now. The stove hardware in Outside Mullinger was 3D-printed. And this past summer, when we worked on the Public's Shakespeare in the Park production of Comedy of Errors, we 3D-printed oversized finials when the supplier failed to deliver in time."
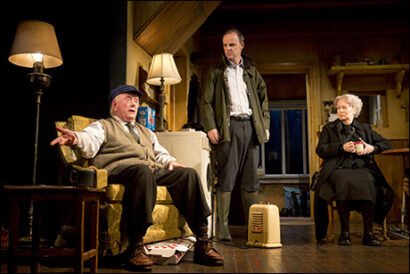