For any revival, the Met production department’s goal is to faithfully re-create the director’s original vision, repairing and updating scenery, machinery, lighting, and other elements as necessary. With Robert Lepage’s groundbreaking production of the Ring, however, that mission was a bit more complicated than usual.
Lepage’s staging relies on what has become known as “the machine,” a 90,000-pound apparatus that comprises 24 30-foot-long aluminum planks suspended between two 26-foot-tall steel towers, plus the requisite machinery to make the planks rise, fall, and spin. An ingenious piece of stagecraft, the machine incorporates several complex systems that must operate in perfect harmony. A heavy-duty, 1,700-psi hydraulic system raises, lowers, and rotates a central axle (known as the “core”) to which all the planks are connected, while pneumatic brakes individually engage or disengage each plank, determining whether it rotates with the core or spins independently. The system also relies on gravity, by way of weights manually inserted or removed from either end of each plank to control the direction of rotation when a plank is disengaged from the core. The final ingredient is manpower, in the form of stagehands positioned behind the machine with ropes, who manually control the movement of the planks when more organic choreography is required. All in all, as Met Technical Director David Feheley explains, the machine is “half animated, half ‘manimated,’ and much more like a giant puppet than an automated set piece.”
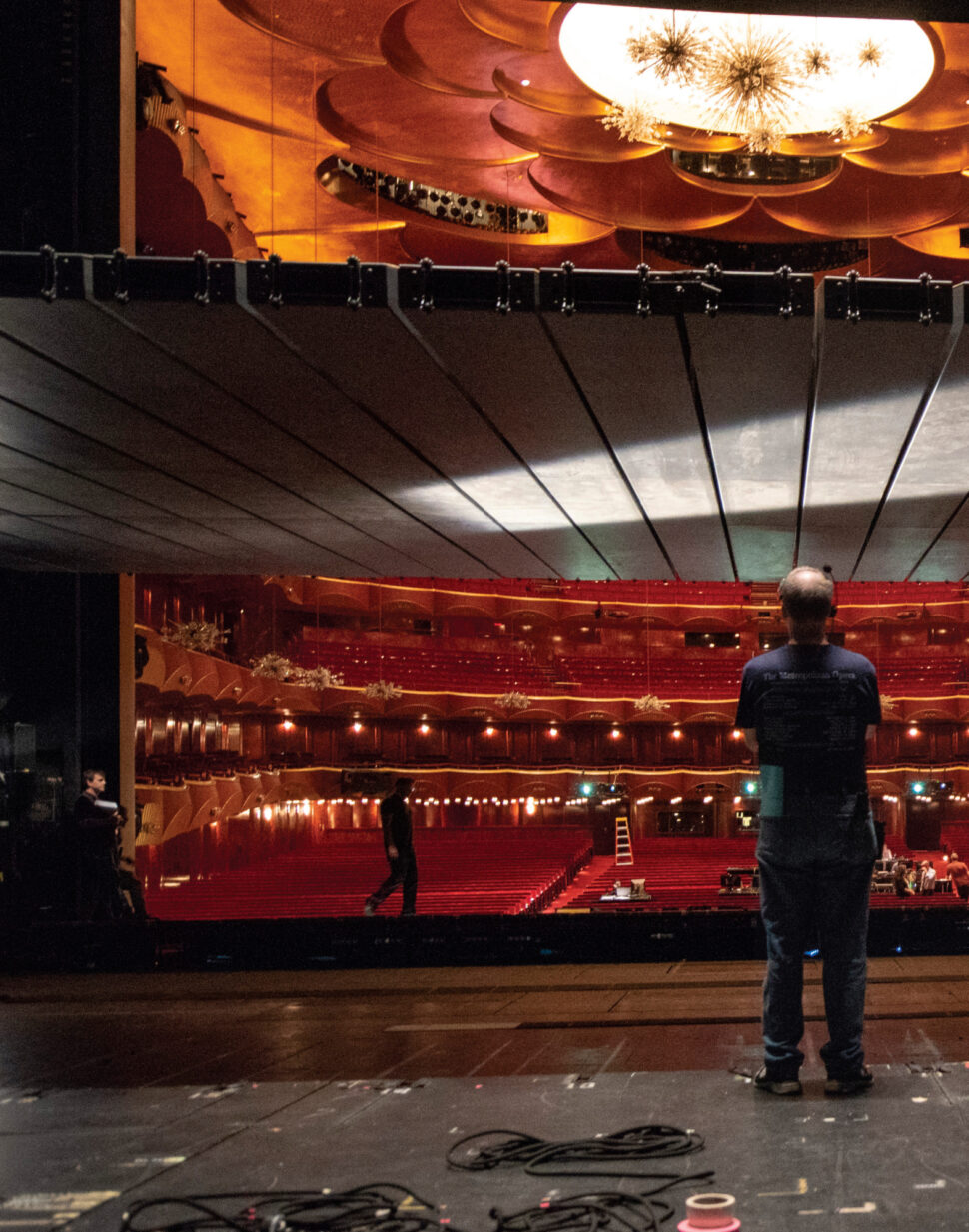
Meanwhile, as the machine transforms itself into myriad different arrangements, cutting-edge projections and lighting effects provide color, texture, and detail, allowing all of Wagner’s fantastical settings—from the cavernous depths of Nibelheim to Brünnhilde’s flame-encircled mountaintop—to materialize on the Met stage. Breathtaking three-dimensional projections adjust in real time, distorting themselves as the machine moves so that the image remains steady despite the motion of the projection surface. The images also respond interactively to the sound of the music and the movement of the singers, using infrared tracking and locator beacons worn by the cast.
When the production was new, much of the technology necessary to make Lepage’s vision a reality did not exist or had never been used in the theater. Control software for the machine’s precisely choreographed transformations had to be written from scratch, and many of the projection methods were being used onstage for the very first time. The staging was operating at the very edge of what was possible, and some intermittent technical difficulties had to be overcome. In the ensuing years, however, technology has caught up with Lepage’s production, and over the past 11 months—thanks to the generosity of Met Board Chairman Ann Ziff, who funded the production when it was new and is now supporting the revival—the Met has taken advantage of these advances to make the staging more consistent and reliable.
Preliminary mechanical and programming tasks began in October 2017, and by March 2018, the production department was ready to begin full-scale work. But the company’s only space large enough to fully assemble the machine and its associated equipment is the auditorium of the opera house—which, of course, was not available for several months of devoted Ring maintenance. So the machine was moved from storage into a rented 23,700-square-foot warehouse in Middletown, New York, where the Met’s stagehands and technical staff spent the first few weeks turning the vast empty space into a working replica of the Met stage. In addition to reassembling the 45-ton machine, this meant setting up its massive hydraulic and pneumatic tanks and pumps that, at the opera house, are installed in the building’s deepest sub-basement; building scaffolding for the multiple video projectors to perfectly match their angle and orientation to the machine in the house; using rolling platforms to mimic the Met’s stage lifts; and installing all of the computer-based control systems that tell the machine how and when to move, and manage what is being projected onto its surface.
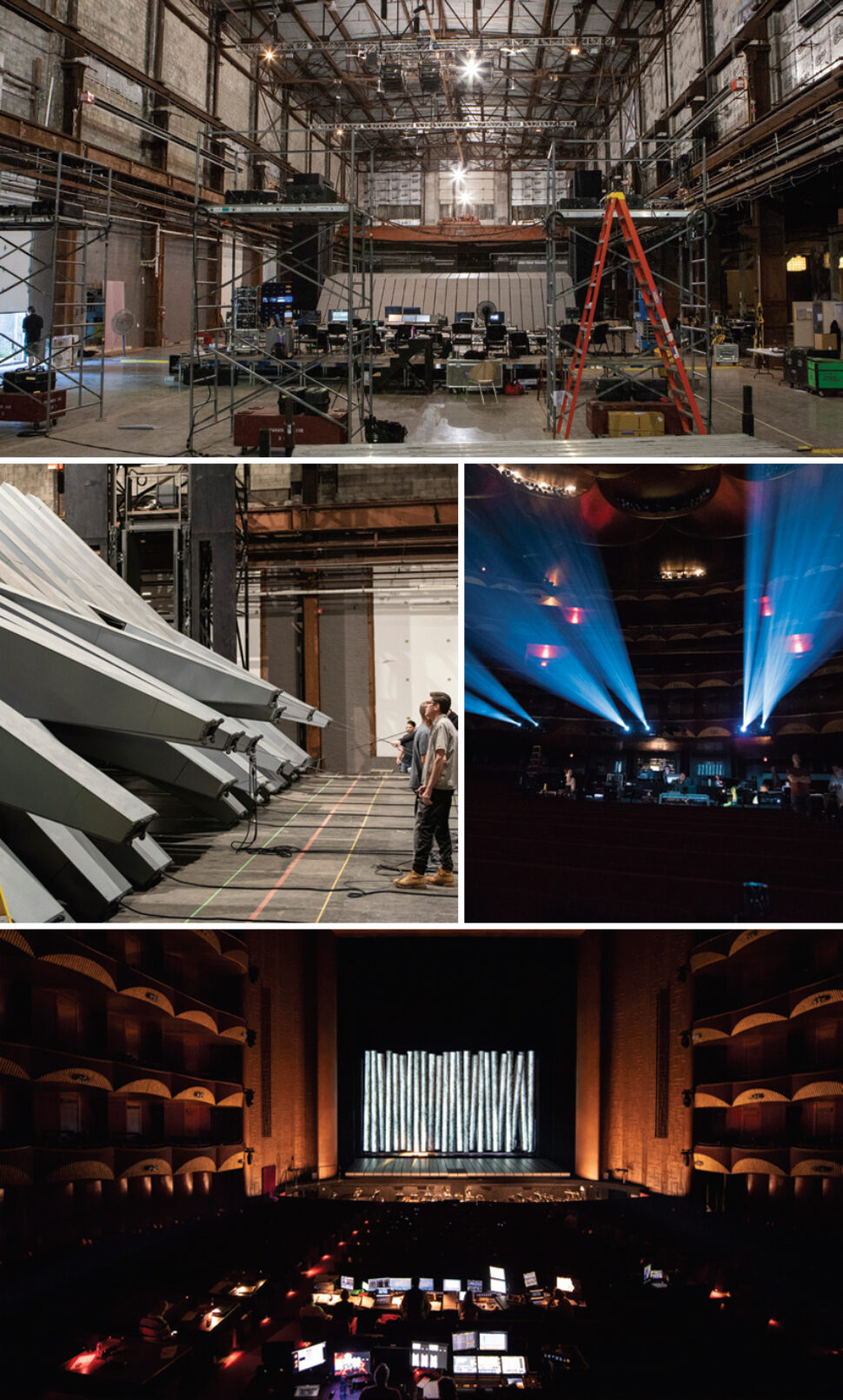
Once everything was functional, Met staff could move on to the real work—updating and improving the production’s mechanical and automation systems. For the mechanical portion, the focus was on making the machine operate as quietly as possible. During previous runs, several factors contributed to unwanted noise during performances. Over time, debris accumulated inside the planks, creating a rain-stick effect when they rotated. To combat this, the inside surfaces of the planks were sprayed with an adhesive coating to catch any loose material. Inside the towers, shims were added to keep the core in balance as it rises and falls, reducing or eliminating the squeaks and groans of metal rubbing metal. And a new assembly methodology was developed to ensure that everything is kept tightly and precisely in place despite the frequent moves required by the Met’s repertory performance schedule.
On the automation front, the bulk of the work consisted of migrating from the original, custom-built control software to new, commercially available versions that offer increased reliability and sophistication. As a result, the movements of the machine and of the Met’s other stage technology can now be integrated. For example, the planks can be rotated downward, moving into a space created by the lowering of the stage lifts, while acrobats, flown on wires, interact with the moving scenery, all as part of one synchronized, automated operation rather than separate movements cued by separate people. The positions of the planks and the status of their individual brakes are also now monitored automatically at all times rather than relying on human-observed safety checks.
In August, with all of the maintenance and updates successfully completed, the machine made its way to the Met for final onstage calibration and testing, after which it was given a clean bill of health and verified as ready for its anticipated return. It has been a long journey to prepare Lepage’s production for its revival, but all of this work will be rewarded next month when an outstanding cast climbs onto the newly restored machine to bring Wagner’s masterpiece to life, set against some of the most dazzling stage spectacles ever created.